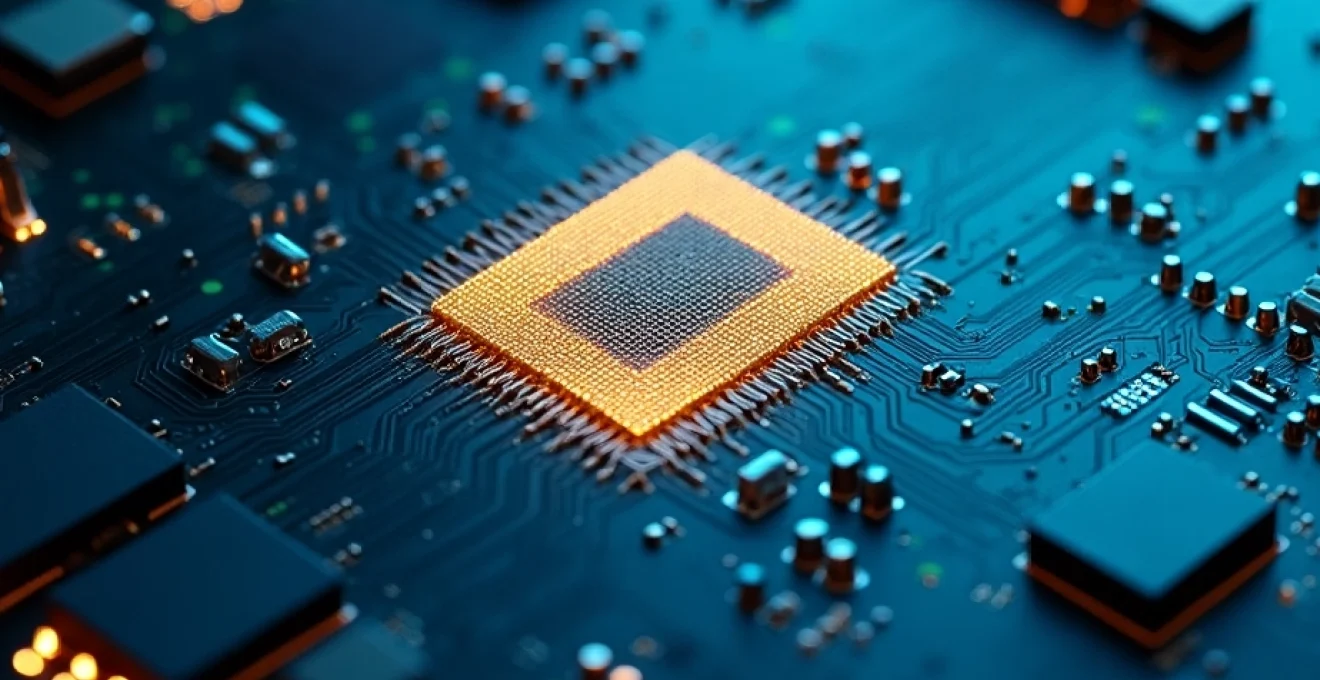
L’evoluzione dell’elettronica moderna ha portato a una crescente domanda di dispositivi sempre più compatti e potenti. In questo scenario, le microvie e i PCB ad alta densità di interconnessione (HDI) emergono come tecnologie chiave per soddisfare le esigenze di miniaturizzazione e prestazioni elevate. Queste innovazioni stanno ridefinendo i confini della progettazione elettronica, consentendo la creazione di dispositivi più sottili, leggeri ed efficienti che mai. Dall’industria degli smartphone ai sistemi avanzati di telecomunicazione, le microvie e i PCB HDI sono diventati elementi indispensabili per spingere l’innovazione tecnologica verso nuovi orizzonti.
Tecnologia delle microvie: principi e applicazioni in PCB HDI
Le microvie rappresentano una vera e propria rivoluzione nel campo dei circuiti stampati. Si tratta di fori di interconnessione estremamente piccoli, tipicamente con un diametro inferiore a 150 micrometri, che consentono di collegare diversi strati di un PCB in modo molto più efficiente rispetto alle tradizionali vie passanti. Questa tecnologia è fondamentale per la realizzazione di PCB HDI, che si caratterizzano per un’elevatissima densità di interconnessioni e componenti.
L’utilizzo delle microvie permette di ottimizzare lo spazio disponibile sulla scheda, riducendo significativamente le dimensioni complessive del circuito stampato. Ciò si traduce in dispositivi elettronici più compatti, leggeri e con prestazioni migliorate. Inoltre, le microvie consentono di realizzare percorsi di segnale più corti, riducendo le interferenze elettromagnetiche e migliorando l’integrità del segnale ad alte frequenze.
Processo di fabbricazione delle microvie con laser CO2
Il processo di fabbricazione delle microvie richiede tecnologie avanzate e precisione estrema. Una delle tecniche più utilizzate è la foratura laser, in particolare con laser CO2. Questo metodo offre numerosi vantaggi rispetto alle tecniche di foratura meccanica tradizionali:
- Maggiore precisione e ripetibilità
- Capacità di realizzare fori di diametro estremamente ridotto
- Riduzione dei danni al materiale circostante
- Possibilità di forare materiali difficili da lavorare meccanicamente
Il processo inizia con la selezione accurata dei materiali dielettrici e dei fogli di rame che comporranno il PCB. Il laser CO2 viene quindi utilizzato per vaporizzare il materiale dielettrico nei punti prestabiliti, creando le microvie. La precisione del laser consente di ottenere fori perfettamente circolari e con pareti lisce, essenziali per garantire una corretta metallizzazione successiva.
Microvie stacked e staggered: confronto prestazionale
Nella progettazione di PCB HDI, è possibile utilizzare diverse configurazioni di microvie per ottimizzare le prestazioni e l’affidabilità del circuito. Le due principali tipologie sono le microvie stacked (impilate) e staggered (sfalsate).
Le microvie stacked sono sovrapposte verticalmente, creando un collegamento diretto tra più strati del PCB. Questa configurazione offre il percorso più breve per il segnale, riducendo al minimo l’induttanza parassita. Tuttavia, può presentare sfide in termini di affidabilità a lungo termine, soprattutto in presenza di stress termici ripetuti.
Le microvie staggered, d’altra parte, sono disposte in modo sfalsato tra i vari strati. Questa configurazione, sebbene leggermente meno efficiente in termini di percorso del segnale, offre una maggiore robustezza meccanica e una migliore distribuzione dello stress termico. È spesso preferita in applicazioni che richiedono elevata affidabilità e resistenza alle vibrazioni.
La scelta tra microvie stacked e staggered dipende dalle specifiche esigenze del progetto, bilanciando prestazioni elettriche, affidabilità meccanica e considerazioni termiche.
Materiali dielettrici avanzati per microvie ad alte prestazioni
La selezione dei materiali dielettrici gioca un ruolo cruciale nelle prestazioni delle microvie e dei PCB HDI. I materiali tradizionali come l’FR-4 stanno lasciando il posto a dielettrici avanzati che offrono caratteristiche superiori in termini di costante dielettrica, fattore di dissipazione e stabilità termica.
Alcuni dei materiali più promettenti per applicazioni ad alte prestazioni includono:
- Resine epossidiche modificate con alta Tg (temperatura di transizione vetrosa)
- Materiali ceramici a bassa perdita
- Polimeri a cristalli liquidi (LCP)
- Substrati in PTFE (politetrafluoroetilene) rinforzati
Questi materiali consentono di realizzare microvie con prestazioni elettriche eccezionali, mantenendo al contempo un’elevata affidabilità anche in condizioni operative estreme. La scelta del materiale dielettrico deve essere attentamente valutata in base alle specifiche del progetto, considerando fattori come la frequenza operativa, le condizioni ambientali e i vincoli di costo.
Progettazione di PCB HDI con microvie
La progettazione di PCB HDI con microvie richiede un approccio completamente diverso rispetto ai circuiti stampati tradizionali. La complessità e la densità delle interconnessioni richiedono strumenti software avanzati e una profonda comprensione delle regole di design specifiche per questa tecnologia. Per approfondire le tecniche di progettazione HDI, clicca qui e scopri le migliori pratiche del settore.
Software CAD specializzati: Altium Designer e Cadence Allegro
Per affrontare le sfide della progettazione HDI, è essenziale utilizzare software CAD specializzati che offrano funzionalità avanzate per la gestione delle microvie e delle regole di design complesse. Due dei pacchetti software più diffusi nel settore sono Altium Designer e Cadence Allegro.
Altium Designer offre un ambiente di progettazione integrato con potenti strumenti per la creazione e l’ottimizzazione di PCB HDI. Le sue funzionalità includono:
- Gestione avanzata degli stackup con supporto per microvie
- Routing automatico con ottimizzazione per HDI
- Analisi di integrità del segnale in tempo reale
- Verifica delle regole di design specifiche per HDI
Cadence Allegro, d’altra parte, è noto per la sua robustezza e scalabilità, rendendolo particolarmente adatto per progetti HDI di grandi dimensioni e alta complessità. Offre funzionalità come:
- Supporto per microvie stacked e staggered
- Strumenti avanzati di fan-out per package BGA
- Analisi termica e di signal integrity integrate
- Collaborazione team-based per progetti complessi
La scelta del software dipenderà dalle specifiche esigenze del progetto e dalle preferenze del team di progettazione. Entrambi gli strumenti offrono capacità avanzate per affrontare le sfide uniche della progettazione HDI con microvie.
Regole di design per l’ottimizzazione delle microvie
La progettazione efficace di PCB HDI con microvie richiede l’aderenza a un set di regole di design specifiche. Queste regole sono fondamentali per garantire la fabbricabilità, l’affidabilità e le prestazioni ottimali del circuito stampato. Alcune delle regole chiave includono:
- Dimensionamento corretto delle microvie in relazione allo spessore del dielettrico
- Mantenimento di un rapporto aspetto (profondità/diametro) adeguato per la metallizzazione
- Gestione accurata delle clearance tra microvie e altri elementi del circuito
- Limitazione del numero di microvie stacked consecutive
- Ottimizzazione della disposizione delle microvie per il controllo dell’impedenza
L’implementazione corretta di queste regole richiede una stretta collaborazione tra il team di progettazione e il produttore di PCB. Molti problemi di fabbricazione possono essere evitati attraverso una comunicazione efficace e l’utilizzo di design for manufacturability (DFM) checks fin dalle prime fasi del progetto.
Tecniche di fan-out e fan-in per package BGA
Una delle applicazioni più critiche delle microvie nei PCB HDI è il fan-out e fan-in dei package BGA (Ball Grid Array) ad alta densità di pin. Queste tecniche consentono di distribuire efficacemente le connessioni da un’area ad alta densità (come un BGA) a un’area più ampia del PCB, facilitando il routing e migliorando l’integrità del segnale.
Il fan-out tipicamente utilizza microvie per portare i segnali dagli strati interni del PCB verso l’esterno, creando più spazio per il routing. Il fan-in, al contrario, utilizza microvie per concentrare le connessioni verso un’area specifica, come un connettore ad alta densità.
Alcune strategie avanzate di fan-out/fan-in includono:
- Utilizzo di microvie stacked per collegamenti diretti multi-layer
- Implementazione di “dog bone” pads per facilitare il routing
- Ottimizzazione della disposizione delle microvie per minimizzare la lunghezza delle tracce
- Bilanciamento tra densità di routing e considerazioni di impedenza
L’applicazione efficace di queste tecniche richiede una profonda comprensione delle caratteristiche elettriche e meccaniche del package BGA, nonché delle capacità di fabbricazione del PCB.
Vantaggi dei PCB HDI con microvie nell’elettronica moderna
L’adozione di PCB HDI con microvie sta rivoluzionando numerosi settori dell’elettronica, offrendo vantaggi significativi in termini di miniaturizzazione, prestazioni e funzionalità. Questi benefici si traducono in dispositivi più potenti, efficienti e compatti, che stanno ridefinendo le aspettative dei consumatori e le possibilità tecnologiche in numerosi campi applicativi.
Miniaturizzazione dei dispositivi mobili: Apple iPhone e Samsung Galaxy
Uno degli esempi più evidenti dell’impatto dei PCB HDI con microvie è nella continua evoluzione degli smartphone. Dispositivi come l’Apple iPhone e il Samsung Galaxy rappresentano lo stato dell’arte nella miniaturizzazione elettronica, con design sempre più sottili e leggeri che integrano una quantità crescente di funzionalità.
L’utilizzo di PCB HDI con microvie in questi dispositivi consente:
- Riduzione significativa dello spessore complessivo del dispositivo
- Aumento della densità di componenti, permettendo l’integrazione di più funzionalità
- Miglioramento delle prestazioni RF per connettività avanzata (5G, Wi-Fi 6, etc.)
- Ottimizzazione del consumo energetico grazie a percorsi di segnale più corti
Ad esempio, l’evoluzione della serie iPhone ha visto una progressiva riduzione dello spessore del PCB interno, passando da circa 0,8 mm nei primi modelli a meno di 0,4 mm negli ultimi, grazie all’impiego massiccio di tecnologie HDI e microvie.
Prestazioni RF migliorate nei sistemi 5G
L’avvento delle reti 5G ha posto nuove sfide alla progettazione di PCB, richiedendo prestazioni RF superiori a frequenze sempre più elevate. I PCB HDI con microvie si sono dimostrati cruciali per soddisfare questi requisiti, offrendo numerosi vantaggi:
- Riduzione delle perdite di segnale grazie a percorsi più corti e diretti
- Miglior controllo dell’impedenza per le linee di trasmissione ad alta frequenza
- Riduzione delle interferenze elettromagnetiche (EMI) tra componenti vicini
- Possibilità di integrare antenne direttamente nel PCB con prestazioni ottimizzate
Questi miglioramenti consentono la realizzazione di dispositivi 5G più compatti, efficienti e con una copertura migliore. Le microvie giocano un ruolo chiave nel routing di segnali ad alta frequenza, permettendo di mantenere l’integrità del segnale anche a frequenze superiori a 28 GHz utilizzate in alcune implementazioni 5G.
Gestione termica avanzata nei processori ad alte prestazioni
Con l’aumento delle prestazioni dei processori moderni, la gestione termica è diventata una sfida critica nella progettazione elettronica. I PCB HDI con microvie offrono soluzioni innovative per affrontare questo problema:
- Utilizzo di microvie riempite in rame per creare percorsi termici efficienti
- Implementazione di piani termici multi-layer per una dissipazione del calore più uniforme
- Possibilità di integrare strutture di raffreddamento direttamente nel PCB
- Ottimizzazione del layout per ridurre i punti caldi (hotspot) sul chip
Queste tecniche consentono di gestire in modo efficace il calore generato da processori ad alte prestazioni, come quelli utilizzati in server data center o workstation grafiche avanzate, mantenendo temperature operative ottimali e prolungando la vita utile
dei dispositivi.
Sfide nella produzione e test di PCB HDI con microvie
Tecniche di ispezione ottica automatizzata (AOI) per microvie
L’ispezione ottica automatizzata (AOI) gioca un ruolo cruciale nel garantire la qualità e l’affidabilità dei PCB HDI con microvie. Tuttavia, le dimensioni ridotte e la complessità delle microvie pongono sfide uniche per i sistemi AOI tradizionali. Per superare queste limitazioni, sono state sviluppate tecniche AOI avanzate specificamente ottimizzate per le microvie:
- Sistemi di imaging ad alta risoluzione con telecamere multiple
- Illuminazione direzionale per migliorare il contrasto delle microvie
- Algoritmi di analisi dell’immagine basati su AI per il rilevamento di difetti submicronici
- Scansione 3D per valutare la profondità e la forma delle microvie
Queste tecnologie consentono di rilevare difetti critici come microvie non completamente forate, problemi di metallizzazione o disallineamenti minimi che potrebbero compromettere le prestazioni del PCB HDI.
Test elettrici: flying probe vs. bed of nails
Il test elettrico dei PCB HDI con microvie presenta sfide uniche a causa dell’alta densità di interconnessioni e delle dimensioni ridotte dei punti di contatto. Due approcci principali vengono utilizzati: il test flying probe e il test bed of nails.
Il test flying probe utilizza sonde mobili che si muovono sulla superficie del PCB per effettuare misurazioni punto a punto. Vantaggi di questo metodo per i PCB HDI includono:
- Flessibilità per testare design complessi senza necessità di fixture dedicate
- Capacità di raggiungere punti di test di dimensioni molto ridotte
- Riduzione dei costi per lotti di produzione piccoli o medi
Il test bed of nails, d’altra parte, utilizza una matrice fissa di sonde che entrano in contatto simultaneamente con tutti i punti di test del PCB. Per i PCB HDI, questo approccio richiede:
- Sonde di precisione con diametri inferiori a 100 μm
- Allineamento ad alta precisione tra PCB e fixture di test
- Tecniche avanzate di controllo della forza per evitare danni alle microvie
La scelta tra flying probe e bed of nails dipende da fattori come il volume di produzione, la complessità del design e i requisiti di throughput del test.
Problematiche di affidabilità: void e delaminazione nelle microvie
L’affidabilità a lungo termine dei PCB HDI con microvie è una preoccupazione critica, specialmente in applicazioni che richiedono elevata durabilità come l’automotive o l’aerospaziale. Due dei problemi più comuni sono la formazione di void e la delaminazione nelle microvie.
I void sono piccole bolle d’aria o spazi vuoti che possono formarsi durante il processo di placcatura delle microvie. Questi difetti possono causare:
- Aumento della resistenza elettrica
- Riduzione della capacità di trasporto di corrente
- Potenziali punti di rottura durante cicli termici
Per mitigare il rischio di void, vengono impiegate tecniche avanzate di placcatura e riempimento, come la placcatura pulsata o l’uso di additivi chimici specifici nel bagno di placcatura.
La delaminazione, ovvero il distacco tra gli strati del PCB, può verificarsi a causa di stress termici o meccanici. Nelle microvie, questo fenomeno è particolarmente critico e può portare a:
- Interruzione delle connessioni elettriche
- Infiltrazioni di umidità e conseguente corrosione
- Riduzione della resistenza meccanica complessiva del PCB
Per prevenire la delaminazione, è fondamentale una attenta selezione dei materiali, l’ottimizzazione dei cicli termici durante la fabbricazione e l’implementazione di design che distribuiscano uniformemente lo stress meccanico.
Tendenze future e innovazioni nelle microvie per PCB HDI
Microvie riempite in rame per interconnessioni ad alta corrente
Una delle tendenze più promettenti nel campo dei PCB HDI è l’utilizzo di microvie completamente riempite in rame. Questa tecnologia offre vantaggi significativi rispetto alle microvie tradizionali, soprattutto in applicazioni che richiedono elevate capacità di trasporto di corrente. I principali benefici includono:
- Aumento della capacità di corrente fino al 300% rispetto alle microvie standard
- Miglioramento della dissipazione termica
- Maggiore affidabilità in condizioni di stress termico e meccanico
- Possibilità di realizzare interconnessioni verticali dirette tra più strati
Le microvie riempite in rame stanno trovando applicazione in settori come l’automotive elettrico, dove la gestione di correnti elevate è critica per le prestazioni e la sicurezza dei veicoli.
Integrazione di componenti embedded con tecnologia microvia
L’integrazione di componenti embedded nei PCB HDI rappresenta un’altra frontiera dell’innovazione. Questa tecnica prevede l’incorporazione di componenti attivi e passivi direttamente all’interno degli strati del PCB, utilizzando le microvie per creare interconnessioni tridimensionali. I vantaggi di questo approccio includono:
- Ulteriore riduzione delle dimensioni complessive del dispositivo
- Miglioramento delle prestazioni elettriche grazie a percorsi di segnale più corti
- Aumento della densità di integrazione dei componenti
- Maggiore protezione dei componenti critici da fattori ambientali
L’integrazione di componenti embedded sta aprendo nuove possibilità in campi come i dispositivi medici impiantabili, dove la miniaturizzazione e l’affidabilità sono parametri critici.
Sviluppi nella fabbricazione additiva di PCB HDI con microvie
La fabbricazione additiva, o stampa 3D, sta emergendo come una tecnologia potenzialmente rivoluzionaria per la produzione di PCB HDI con microvie. Questa tecnica offre diversi vantaggi rispetto ai metodi di fabbricazione tradizionali:
- Maggiore flessibilità nel design, consentendo geometrie complesse e personalizzate
- Riduzione dei passaggi di produzione e dei tempi di prototipazione
- Possibilità di creare strutture tridimensionali integrate
- Potenziale per la produzione on-demand e la personalizzazione di massa
Attualmente, la ricerca si sta concentrando sullo sviluppo di materiali conduttivi e dielettrici adatti alla stampa 3D che possano soddisfare i rigorosi requisiti dei PCB HDI. Sebbene questa tecnologia sia ancora nelle fasi iniziali, ha il potenziale per rivoluzionare il modo in cui vengono progettati e fabbricati i PCB HDI del futuro.